Blog article
Energy technology in battery cell production: Efficiency, innovation, sustaina-bility
What characterises battery cell production in Europe, and more precisely in Germany? And what role does the energy technology sector play in this? Battery cell production is playing an increasingly important role in the European Union's (EU's) direction and has a significant influence on the EU's self-image. Efficient and sustainable battery cell production is an important building block for the EU to achieve the goals of the "European Green Deal" for 2030. The main challenges lie in the additional amount of energy required. Currently, a battery capacity of 1 kWh is expected to require 30 to 55 kWh of electricity for battery production. This amount of energy also needs to be covered in a climate-friendly and energy-efficient manner. The framework conditions for this are provided by the Renewable Energy Sources Act (EEG) and the Energy Effi-ciency Act (EnEfG). To achieve these goals and at the same time create an alternative to existing production sites, it is the task of energy technology to understand the high energy costs and climate-friendly production as an opportunity and unique selling point for Europe and Germany in particular. The tasks lie in increasing energy efficiency and utilising renewable energies, which can be achieved by developing an energy concept.
As climate change progresses, it is essential to reduce emissions across all systems, optimise existing structures and processes and break new ground. To fulfil the national and EU-wide climate targets, all sectors must achieve savings, with the electrification of transport playing a central role. This sector was responsible for a quarter of total emissions in the EU in 2019, which is why there is great potential in electrification. This potential has already been recognised, which is why a production capacity of 400 GWh of batteries is planned in Germany alone by 2030. But why do battery cell manufacturers now need to develop concepts for savings and optimisation? Battery cell production is an energy-intensive sector.As climate change progresses, it is essential to reduce emissions across all systems, optimise existing structures and processes and break new ground. To fulfil the national and EU-wide climate targets, all sectors must achieve savings, with the electrification of transport playing a central role. This sector was responsible for a quarter of total emissions in the EU in 2019, which is why there is great potential in electrification. This potential has already been recognised, which is why a production capacity of 400 GWh of batteries is planned in Germany alone by 2030. But why do battery cell manufacturers now need to develop concepts for savings and optimisation? Battery cell production is an energy-intensive sector.
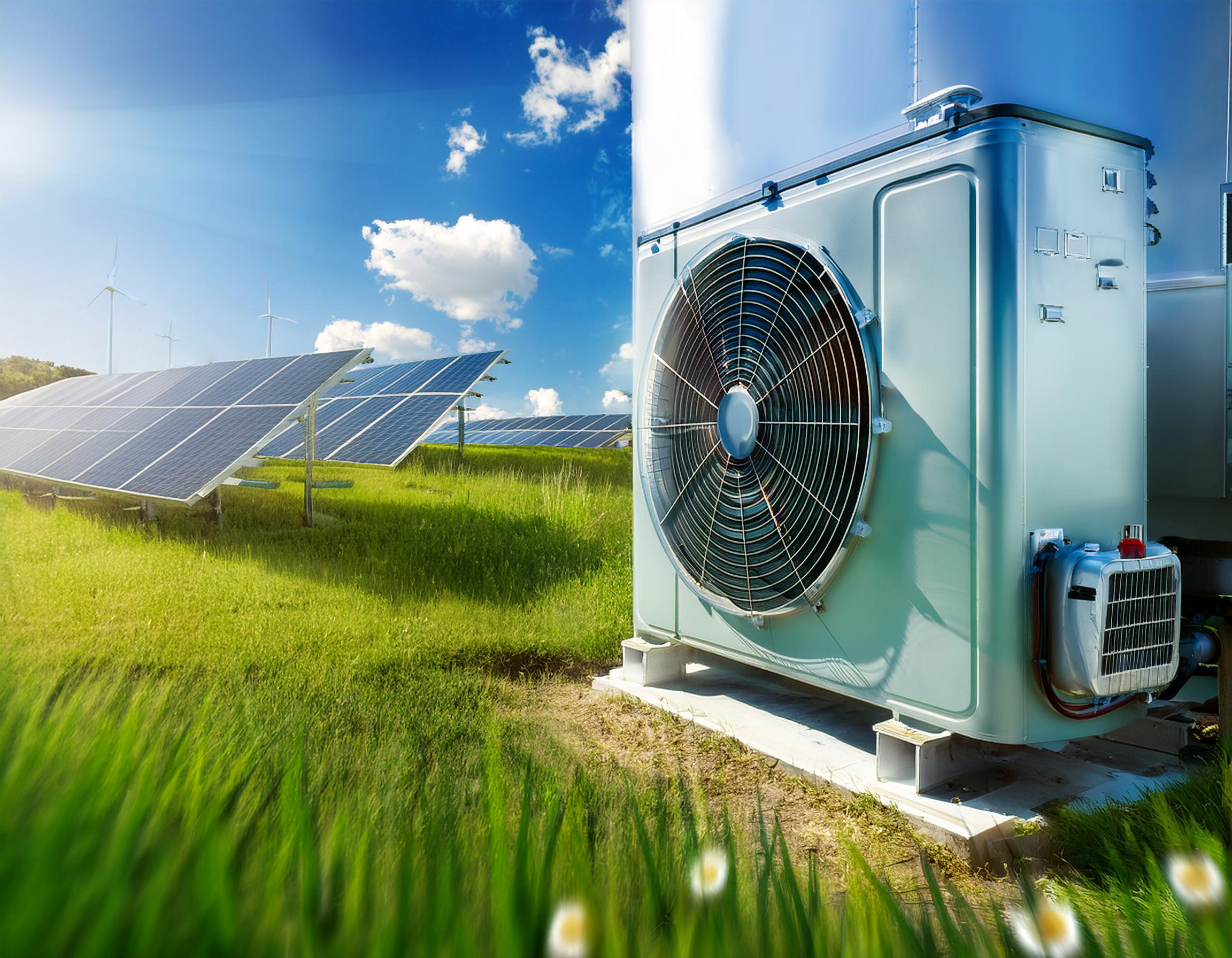
Political framework conditions and their significance for the energy technology sector
The additional amount of energy required for production for the planned production capacity amounts to 20 TWh per year. For the German electricity mix from the year 2022, this corresponds to of 8.7 million tonnes. At an international level, this figure is many times higher, which is why the political framework conditions are particularly relevant for this industry. In Germany, the EEG and the EnEfG stand out. The EEG has had a decisive influence on work in the field of energy technology since 2000. Here, renewable electricity sources are favoured and purchased at a fixed price. This is intended to support the transformation of electricity generation. This also increases the incentive for electricity-intensive sectors and companies to generate and store electricity themselves. This has a major impact on the creation of an energy concept. Another important factor is the EnEfG, which comes into force in 2023. This formulates binding final and primary energy saving targets for the first time, whereby, among other things, final energy consumption is to be reduced by almost 27 per cent by 2030 compared to 2008. As a result, existing processes must be optimised with the help of energy management systems and outgoing energy flows such as waste heat must be better integrated into the process to reduce overall energy consumption. The Energy Technology department plays a decisive role here, as energy-efficient battery production fuelled by renewable energies not only pursues ecological goals, but also represents a unique economic selling point.
Energy technology in the development of an energy concept for battery cell production
In energy technology, all energy-related aspects of battery cell production are considered. This includes the generation, conversion, transport, storage, and utilisation of energy. In order to gain an overview, an energy concept is developed for this purpose. A basic process for developing an energy concept for battery cell production consists of the following four points:
- Input determination
- Load profile generation
- Producer comparison
- Energy concept
Input determination
When determining the input, the production concept is determined with all machine data over the course of a year to obtain a data-based foundation and overview. Based on this, a load profile can be generated. The most energy-intensive process steps are drying the electrodes, which accounts for 43 per cent of total energy consumption, and maintaining the drying room conditions, which accounts for 39 per cent. In factories with continuous production, this amounts to around 1,800 GWh per year. One reason for this is drying, which requires high temperatures of up to 200 °C and drying room conditions between 0 °C and -70 °C with a high-volume flow.
Load profile generation
A load profile summarises all areas that consume energy over the course of a year. The amount of electricity, heating and cooling required by the processes and the building is summarised. The load profile can then be used to determine a suitable mix of energy producers. In the area of electricity procurement, a distinction can be made between internal and external energy: Whilst internal energy refers to energy generated internally, for example by solar or wind power, external energy refers to energy purchased externally from the electricity grid.
Producer comparison
There is a wide range of energy generators to choose from: Chillers and heat pumps can be used here, high temperatures can be generated by direct current or gas boilers, or energy can also be generated secondarily from waste heat to utilise the necessary temperatures. Energy can also be generated with secondary energy production from waste heat. Wastewater, compressed air generation, recovery from electrode drying or the heat generated during in-house power generation can be sources. The heat can then be stored thermally for later use, like electricity storage.
Energy concept
The energy concept is the centrepiece, as all energy-consuming and energy-generating factors and their interaction are mapped there. Areas that need to be optimised can be identified there and what effect a possible optimisation would have on the entire system. Possible areas for optimisation include the process, energy procurement and the basic monitoring of the entire process.
Energy concept for efficient and sustainable battery cell production
In the process, the most energy-intensive steps mentioned above are the main ones that can be addressed. Alternative drying processes, such as laser or induction drying, as well as new concepts such as coating without solvents are promising options. When creating the drying room conditions, the system can be optimised using a highly efficient combined heat pump can reduce primary energy consumption by up to 40 per cent. The concept can also be rethought here. For example, the integration of minienvironments can drastically reduce the volume to be dried. The efficiency of the heat provided by the dehumidification technology in the drying rooms can be attributed to two factors: Firstly, the combi-heat pump always generates cooling and heat simultaneously, so that this utilises the waste heat from cooling as a source of heat generation. Secondly, a system temperature of 85 °C, which can be supplied by the heat pump, can be achieved by using three dehumidification rotors connected in series.
In the area of energy procurement, this does not just mean the pure purchase or production of energy. With the help of load management, for example, the load profile can be analysed, and peak loads identified, which can then be reduced or intercepted in subsequent steps. One way of doing this is to utilise electricity storage systems. If possible, this stores the internal energy and is used during peak loads. This allows costs to be reduced and self-generated energy to be utilised to a large extent. Finally, around digitalisation, advancing automation, digital twins and data-based simulations can reduce errors and make processes more efficient.
After optimisation, the energy concept clearly shows the resulting effects. It also shows whether optimisation in one area has a negative impact on other areas. Expressed in figures, an optimised system can reduce primary energy requirements by up to 40 percent. This corresponds to a saving of €136 million per year at an electricity price of February 2024 and the electricity consumption of battery cell production. Overall, the relevance and areas of responsibility of energy technology in battery cell production, which implements environmental policy goals, develops sustainable concepts and is also responsible for the considerable cost factor of energy, are evident.
Last modified: