Blog article
First prototype cells successfully loaded
The initial prismatic FFB prototype cells have been successfully produced. Last year, a research consortium within sub-project 2 of the "FoFeBat" initiative, supported by the German Federal Ministry of Education and Research, developed and constructed a novel prototype cell. In April 2024, these cells were filled and formed for the first time at the Battery Abuse Center (BAC) of the PEM Chair at RWTH Aachen University, marking the completion of the first prismatic cell construction.
There is great interest in prismatic cells, particularly in the automotive industry: Firstly, because they can be better integrated into the cell-to-pack process than pouch cells, despite the heavy metal housing. This eliminates the need for heavy support and safety structures in the battery pack. Overall, packs built with prismatic cells can be lighter than packs with pouch cells. On the other hand, they are safer precisely because of this housing, and the heat in the cell is distributed more evenly.
The innovation of the prismatic FFB cell design lies primarily in the shape of the electrodes: instead of electrode coils, electrode stacks were used in the prismatic cell. In addition to better heat distribution, the advantages are lower resistance in the cell, homogeneous pressure distribution, and a lower risk of deformation;
Prismatic prototype sprint: The production process chain of the first FFB prototype cells
Following the theoretical conception of the electrode and cell designs, the development of the prismatic FFB prototype cells took another major step forward in the first half of this year. The production of the cells can be seen as a joint success of the German battery research ecosystem, as the process chain in the case of the "prismatic prototype sprint", as the cell production was christened within the project, can be depicted as a journey across Germany. This involved six stations:
First station: Production of the cup and lid assembly
At Fraunhofer IGCV in Augsburg, the lid assemblies and the cups were manufactured. The cups were produced for the first time using selective laser melting (SLM) - a 3D printing process in which the physical object is produced by melting a metallic powder using a laser. Due to its flexibility, the process is particularly suitable for the construction of prototypes. After printing, the components were post-processed to guarantee dimensional and shape accuracy.
The cover assembly is made up of a base plate, two busbars, an insulating rail, and two terminals. These components create the connection between the power source/sink and the electrodes in the final battery cell (refer to the illustration). To ensure the cell is sealed, the terminals were attached to the outside using a resin bed for electrical insulation. The filling hole for the electrolyte in the base plate was placed in the middle to accommodate the filling system requirements.
Second station: Production of the electrode material
The electrode material was manufactured at two different locations in Germany: The cathode coils were ordered from UniverCell in Flintbek (Schleswig-Holstein), while the anode coils were produced in Münster. Since the cathode materials are very sensitive and sometimes toxic, a special production environment is needed for their processing. This environment will be available in the "FFB PreFab", but it could not be provided at the time of production. Therefore, their production was outsourced to the cell manufacturer UniverCell. However, it will also be possible to independently carry out production in the "FFB PreFab" by the end of 2024. The anode foils were coated and dried in the "FFB Workspace", followed by calendering at the MEET-Batterieforschungszentrum and quality testing.
Third station: Stacking the electrode foils
Part of the assembly of the cells was carried out manually: at the Fraunhofer IGCV, the electrode sheets were first separated mechanically using steel rule dies. Then a research assistant at Fraunhofer FFB stacked them by hand in a specially designed stacking device. The electrode stacks were then hot-pressed again and fixed in place with tapes (see Figure 4). The hydraulic hot press presses the cell stack with a pressure of 150 kN, which results in the coating of the separator and electrode being laminated together. The laminated cell stack is wrapped with an additional plastic separator layer and fixed with adhesive tape to protect the electrodes from contamination.
Fourth station: Contacting the terminals with the electrode foils
As part of the cell development, an innovative contacting concept was developed that enables a space-saving and high-performance connection of the electrodes to the cover assembly. The real electrode stacks were welded together with the busbars of the cover assembly using ultrasonic welding at the Welding and Joining Institute ISF in Aachen (see Figure). New contours of the ultrasonic welding tools (sonotrode and anvil) were also tested during this process.
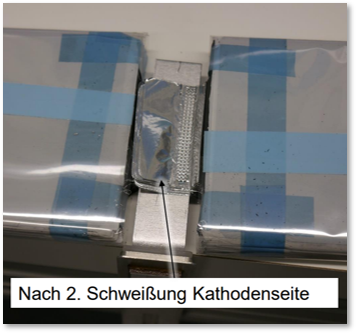
Fifth station: cell assembly and welding
After making contact, the cell stack and housing came together for the first time at the Institute for Machine Tools and Industrial Management IWB at the Technical University of Munichfor cell assembly. The assembly made it clear once again that every millimeter counts when positioning the cell stack and busbar. The individual parts came together to form a cell, which proved to be sufficiently tight and strong after being welded by a laser.
The final in Aachen: Electrolyte filling and forming
The welded prototype cells traveled to the PEM chair at RWTH Aachen, where they were filled with electrolyte in a vacuum chamber. A specially designed product carrier was developed for filling the cells. The filling was carried out in three steps, adapted to the cell design and system technology. This also gave the electrolyte enough time to completely wet the electrodes - the so-called wetting of the cell.
The final process step took place at the Battery Abuse Center of the PEM in Aachen, where the cells were first formed in a product carrier with live degassing. During the prototype construction, the focus was not on optimizing production times. The sample cells were loaded and unloaded using low currents and C-rates. Additionally, the cell temperature was monitored using a thermal imaging camera and temperature sensors. During the initial formation of the sample cells, the interfaces form on the active material particles (solid electrolyte interface - SEI) to passivate and thus stabilize the electrodes. The capacities achieved by the cells within the cycles corresponded to the calculation models that were set up. At the end of the project, the cells will be further characterized to determine the exact performance of the cells.
After completion, the characterization follows
The construction of the first prismatic FFB cells was successful. The innovative cell design and the associated production steps were evaluated within the process chain. In the next phase of prototype construction, the connection of the electrode stack and the design of the lid assembly will be further optimized. To this end, additional sample cells will be tested in larger quantities to ensure large-scale production.
Researchers from the MEET Battery Research Center at the University of Münster, the Institute for Welding and Joining Technology ISF and the PEM Chair of Engineering of E-Mobility Components at RWTH Aachen University, the Institute for Machine Tools and Business Administration IWB at TU Munich and the Fraunhofer IGCV were involved in prototype construction. Thank you for the excellent cooperation.
Last modified: