Whitepaper "Exploring additional benefits of plastic piping"
Lighter, more durable, more resistant - Do these properties of plastic piping systems also apply to their use in battery cell production? The Fraunhofer FFB, in cooperation with GF Piping Systems, has published a white paper entitled "Plastic piping in battery cell production. A potential analysis for production systems and buildings". It identifies and analyzes potential applications for plastic piping in battery cell production. The whitepaper is the result of a pre-viously conducted study.
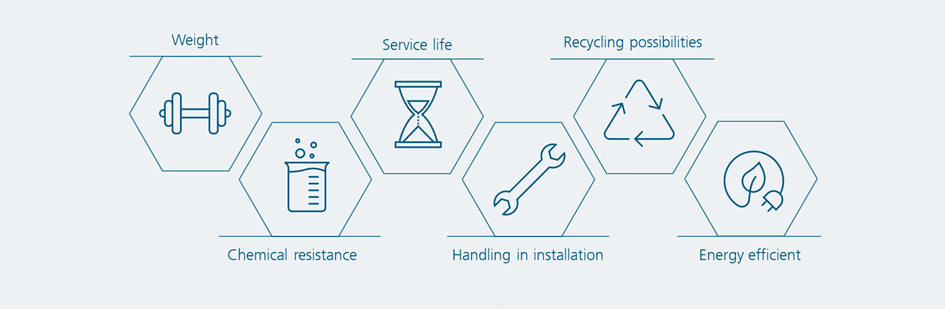

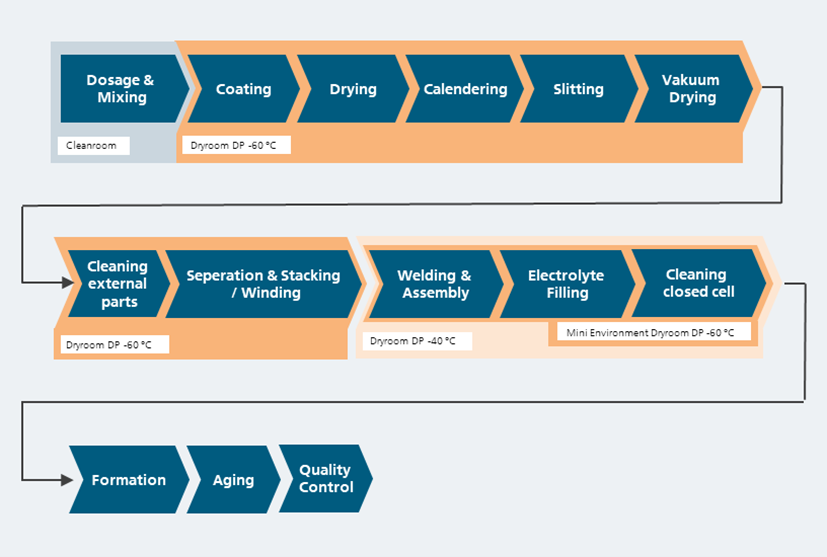
Battery cell production is a growing industry, as it is considered a key technology for the energy and mobility transition in Europe. Until now, production has primarily taken place in China, but the market for e-mobility is now booming in Europe, allowing European companies to gain a foothold in the battery industry. The multi-step manufacturing process offers many companies new points of contact and therefore opportunities to expand their product portfolio. As the scaling of battery cell factories is a major factor in meeting the steadily growing demand, optimization opportunities are also being sought outside of production that will lead to more efficient and sustainable manufacturing. One such could lie in using alternative materials for piping systems: The Whitepaper questions the materials of piping used within the building and equipment and identifies key application areas for flow solutions made of plastics. The combination of expertise in thermoplastics on the part of the project partner GF Piping Systems with expertise in battery cell production on the part of Fraunhofer FFB has led to new findings.
What are the necessary specifications for pipes in a battery factory?
Since the conditions in cell production are very specific at some locations, Fraunhofer FFB has pooled its interdisciplinary expertise to conduct the potential analysis. To do so, we developed a technology management methodology tailored to the requirements of the areas under investigation. Four criteria form the basis on which potentials for plastic piping compared to stainless steel pipes are to be researched - environment, compatibility, market, and value. The environment in this context refers to the process parameters that could have an impact on plastic pipes, such as pressure and temperature. Under the compatibility criterion, the compatibility of chemical substances with the pipe material is examined. In addition, the value that plastic pipes could add to the process in question is determined.
Furthermore, in addition to the need for piping in a Gigafactory, its area of use, the environmental conditions, and the properties of the transported substances play an essential role. An examination of the individual process steps reveals the following main areas of application: Potential areas of application for piping technology are not only in the field of technical building equipment (TGA) but also especially in clean room and dry room technology as well as in some process steps from electrode manufacturing to forming.
Plastic piping systems are particularly interesting for the mixing process since the environment does not place high demands on the materials here. Thanks to their chemical resistance and smooth surfaces, they are well suited for the transport of granular and liquid raw materials as well as mixed slurry, which can cause corrosion in metal. But systems made of plastic can also help reduce costs and the carbon footprint in clean and dry rooms. The entire process chain has different but specific temperature requirements depending on the process step, which is why the amount of piping for various heating and cooling circuits is enormous. It is precisely in these areas that plastic piping systems can bring about greater environmental friendliness.
Further potentials of plastic components lie in weight, service life, recycling possibilities, installation time, and energy efficiency. The extent to which these also come into play in individual areas of battery cell production is shown in the white paper.
Download Whitepaper:
Last modified: