Blog article
How dry coating is changing battery cell production
As a step in dry processing, dry coating in battery cell production is an innovative process that is revolutionizing traditional electrode production. This approach addresses the issue of how to process dry starting materials into battery electrodes in an efficient, resource-saving and sustainable manner without the use of solvents. Due to the growing demand for batteries for electric vehicles and energy storage systems, manufacturers are increasingly focusing on more efficient and environmentally friendly production methods.
Slurry Based Electrode Coating Process
Traditional battery manufacturing uses a standard slurry-based process to produce battery electrodes, in which the active material, binders, and conductive additives are processed in a solvent to form a suspension, or paste. The slurry is then applied to a thin metal foil, typically copper or aluminum. In the subsequent drying step, the solvent used after coating is evaporated and recovered.
However, the use of solvents and the resulting drying step in electrode production has a number of disadvantages for battery cell production. For example, the drying and solvent recovery systems are capital intensive and take up a lot of space. If the battery is manufactured in countries where electricity and gas costs tend to be higher, such as in Europe, the high energy costs for drying and solvent recovery are an additional complication for manufacturers. In addition, the use of toxic solvents (NMP) in cathode production poses a potential risk to humans and the environment.
Alternative production approach: dry coating
To reduce production costs and enable sustainable production of battery cells, researchers are working on alternative electrode manufacturing processes, such as dry processing. In contrast to conventional electrode production, the starting materials are mixed in a first step in a dry process without solvents (DRY mixing). In the second step, the dry premix is pressed into the electrode using special binders and applied to the current conductor film. The elimination of solvents in the battery cell production process eliminates the energy-intensive drying step.
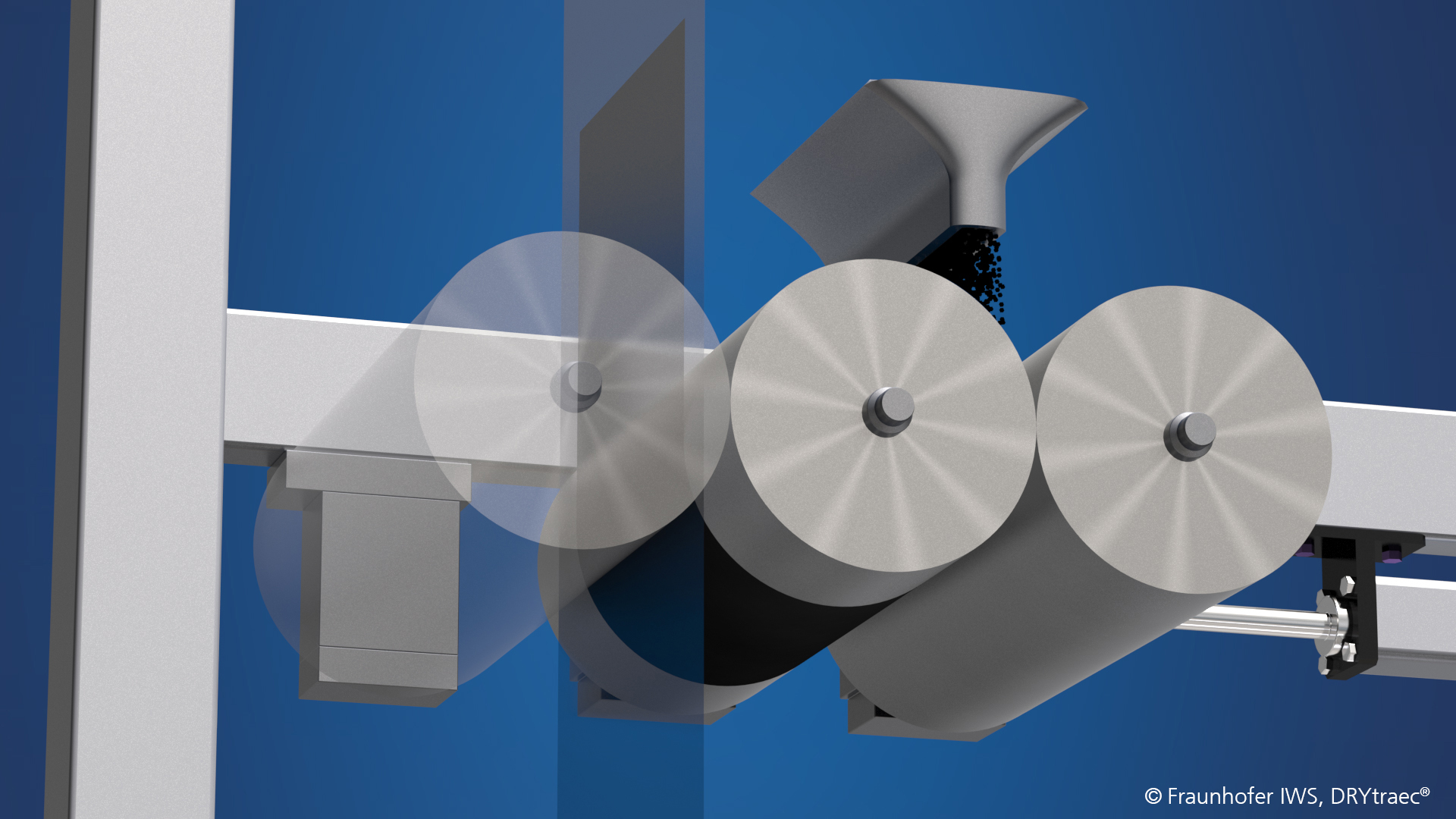
Activities to implement the dry coating system
Together with partners from industry and research, the Fraunhofer FFB is pursuing the goal of further developing the innovative solution and transferring it to an industrially relevant production environment. A direct rolling process developed and licensed by the Fraunhofer Institute for Material and Beam Technology IWS, known as DRYtraec®, is proving to be a stroke of luck for the Fraunhofer FFB. On the one hand, the Fraunhofer IWS team led by Dr. Benjamin Schumm was able to advance the technological process maturity to 5-6. On the other hand, the internal Fraunhofer development enabled a joint cooperation between Fraunhofer FFB and Fraunhofer IWS to further develop the potential of DRYtraec®. In addition, DRYtraec® has already enabled Fraunhofer IWS researchers to celebrate successes in the processing of sulfidic solid electrolytes for the production of solid-state batteries.
As part of the "FoFeBat-Project (TP3)", the Fraunhofer FFB and the Fraunhofer IWS are working to enable the transition of DRYtraec® to a higher process maturity (TRL > 7). By further developing and optimizing DRYtraec®, the research project aims to establish dry coating as the leading method in battery cell production by enabling sustainable, efficient and high-quality production.
To achieve these goals, a pilot scale dry coating plant will be commissioned (for the first time) in 2024 and integrated into the "FFB PreFab" in the second half of 2025. This plant will enable the achievement of higher goals in the future, such as the establishment of higher process speeds of at least 20 m/min with a coating width of 400 mm. In addition, the establishment of a suitable in-line sensor system will help researchers to better monitor and control the coating process.
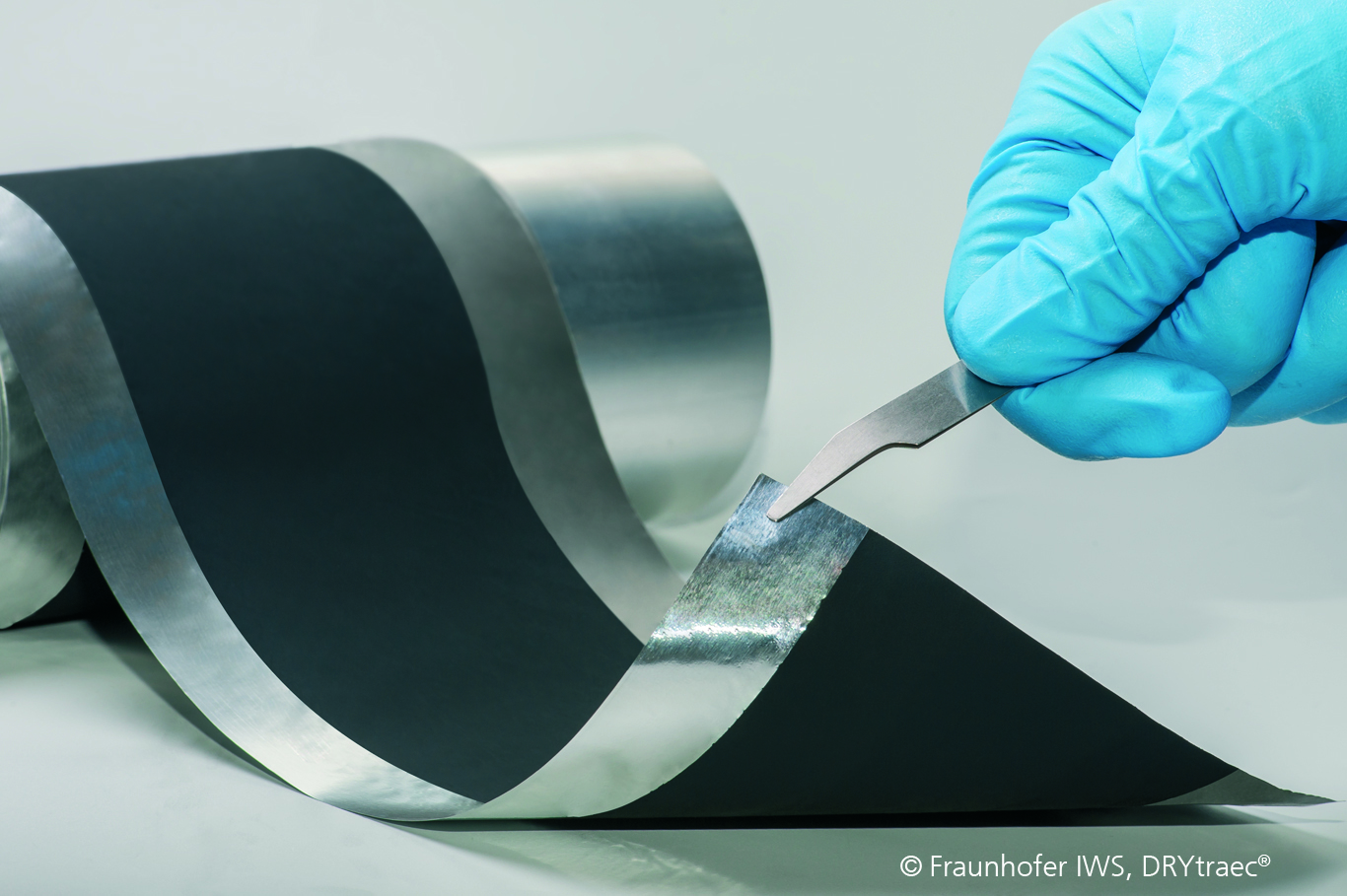
Further process chaining and establishment of analytics at Fraunhofer FFB
Before the material can be processed into electrodes on a dry coating system, it requires the upstream production step of dry mixing. The elimination of solvents in the mixing process will change the processing of the raw materials and the requirements for the plant technology. For this reason, part of the existing mixing plant technology at the Fraunhofer FFB will be retrofitted as early as 2024. This will allow a broader process control and minimize the material wear of the plant components. The first production trials for dry mixing will start in the second half of 2024. At the same time, detailed analytics will be set up in the FFB "PreFab" to check the quality requirements of dry premixes and to better coordinate the two process steps of DRY mixing and coating.
In the future, solutions will be developed along the entire dry processing chain. Starting with dry blending, dosing of dry powder blends on the calender, process linking, analytics or a more comprehensive overview of the entire life cycle analysis.
Last modified: