Battery Use Case, Mini-Environment, Digitization of Battery Cell Production
Fraunhofer FFB presents innovative solutions for battery cell production at the Hannover Messe
The efficient and scalable production of battery cells and packs plays a crucial role in the future of e-mobility. Together with eight partner companies, the Fraunhofer FFB is presenting innovative solutions for industrial battery cell and pack production at the world's largest industrial trade fair (March 31 to April 4, 2025, Hall 6, Booth D62). A model manufacturing process will demonstrate how robot-assisted technologies can optimize production.
Münster. The requirements for battery cell production are constantly changing: flexibility, transparency, and intelligent processes are crucial for the future of e-mobility. For the first time, the Fraunhofer FFB is presenting solutions for industrial battery cell and pack production at the world's leading trade fair for the industry. “Battery research and industrial manufacturing are becoming increasingly complex and multi-layered,” says Dr. Jonathan Krauss, division director of ‘Digitization of Battery Cell Production’ at the Fraunhofer FFB. ”At the same time, competition from Asia requires strategic collaboration in Europe. Only by joining forces can we establish competitive and sustainable battery cell production.”
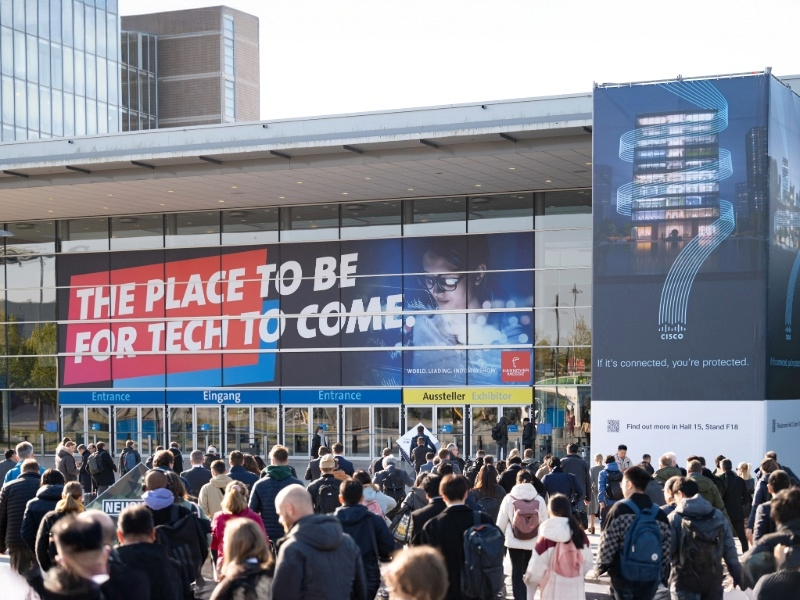
Technological highlights at the exhibition stand
As part of the Battery Use Case at the Hannover Messe, the Fraunhofer FFB, together with Bosch Rexroth, DBR 77, FANUC, IBG, KEYENCE, LENZE, SCHUNK, and Vision Lasertechnik, is designing a visionary demonstration of the battery cell production of the future. The approximately 100 m² demonstrator will show live key steps in EV battery production – from precise cell manufacturing processes to intelligent Re-X recycling. The Fraunhofer FFB is contributing its expertise here, particularly in cell production.
Innovative mini-environment approach for more efficient battery cell production
For the first time, a self-sufficient mini-environment approach is being presented that is integrated into an automated production line to weld prismatic battery cells by laser. “With this transport unit, we are setting a new standard in production technology,” says Marius Heller, research associate in the ‘"Assembly and Formation" group. "Thanks to this system, large clean and dry rooms could be dispensed with in the future, resulting in significant savings in energy and investment costs."
Digital twins and VR: a first-hand experience of battery cell production
In addition to the real construction, the Fraunhofer FFB is also participating on a digital level. With the help of virtual building modeling, the “FFB PreFab” is becoming a tangible open battery cell factory for research and development. To do this, the digital content is incorporated into the digital twin of the company DBR77. “Using digital twins and VR technology, DBR77 and Fraunhofer FFB enable visitors to experience the individual production steps up close and understand how sustainable value chains for battery cell production can be created,” says Dr. Jonathan Krauß.
Workshop of the Battery Cell Technology Cluster: Innovation and Networking
On the third day of the fair (Wednesday, April 2, 2025, 10 a.m.), the Battery Cell Technology Cluster – consisting of Capgemini, Fraunhofer FFB, PEM Motion and the Chair of Production Engineering of E-Mobility Components (PEM) at RWTH Aachen University – invites interested parties to an exclusive, practical four-hour workshop in the Cosmopolitan Restaurant on the exhibition grounds. Dr. Kristina Borzutzki, head of the “Process Engineering” group at the Fraunhofer FFB, will participate in a round-table discussion as an expert. In addition to two keynotes, the event also offers space for intensive networking.
Throughout the week, technical experts from the Fraunhofer FFB will be present at the joint stand (Hall 6, Stand D62) to provide visitors with detailed information and insights into the presented technologies.
Last modified: